
The Fundamentals of Hydraulic Forging Press: How It Works and What You Need to Know
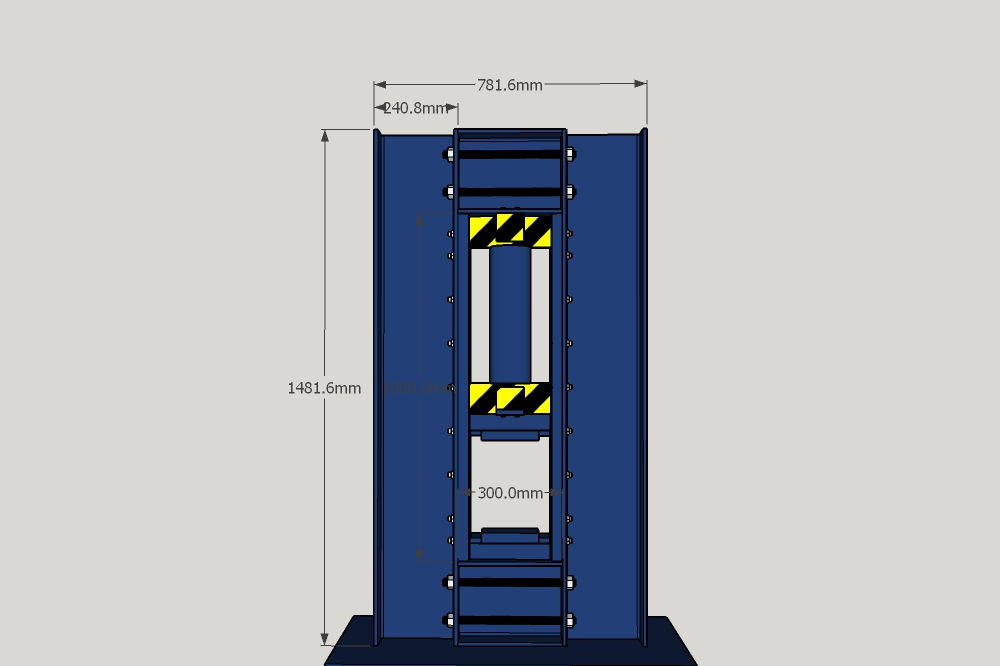
Hydraulic forging press is a type of machine used in metalworking and manufacturing. It is used to shape metal through a process of compressing and forming it under high pressure. The press is equipped with a hydraulic system, which uses a pressurized fluid to generate the forces required for the forming process. The press is versatile and can be used to form a variety of shapes from a range of metals. It is an essential tool for many manufacturing operations, providing precise and consistent results. To get the most out of a hydraulic forging press, it is important to understand its fundamentals. In this article, we will explore the working principle of this machine and the features it needs to have to effectively shape metal. We will also discuss the different types of hydraulic forging presses available on the market and their uses.
What is a hydraulic forging press?
A hydraulic forging press is a machine used to shape and form metal pieces through the use of force and pressure. It is equipped with a hydraulic system, which uses pressurized hydraulic fluid to generate the forces required for the forming process. Because of its ability to apply force in a controlled manner, a hydraulic forging press is used to shape metal pieces that would otherwise be impossible to work with manual tools. A forging press is usually larger and more expensive than an ordinary press because it needs to be able to apply larger forces. A forging press is often used for the initial forming of a part that will then be finished by other means. Forging presses come in a wide variety of types and sizes, with different features and capabilities.
How does a hydraulic forging press work?
The basic components of a hydraulic forging press are the frame, the ram, the hydraulic system, and the die. The frame is the base and support system of the machine which houses other components. The ram is the moving part that is used to apply pressure to the workpiece. The hydraulic system is the mechanical system that pressurizes the working fluid to operate the press. The die is the metal piece that is used to shape the workpiece. In a forging process, the metal piece being shaped is placed between the die and the ram so that it is being compressed by the ram from above and the die from below. As the pressurized working fluid is pumped into the hydraulic system, it forces the ram to move towards the die, exerting immense pressure on the metal piece and forming it into the desired shape. The hydraulic forging press uses the hydraulic system to operate the press and pressurize the pressurized fluid. The hydraulic system is a closed system and is used to prevent the escape of the pressurized fluid.
Benefits of using a hydraulic forging press
– Large force applied to a small area – A forging press can apply a great amount of force to a small area, enabling a part to be formed with great accuracy. This is especially useful when making small parts that need to be formed with precision. – High consistency – Due to the fact that the amount of force applied to the metal piece is controlled by a hydraulic system, the press is able to apply the same amount of force each time, providing the operator with high consistency. – Ability to work with difficult materials – A forging press is able to work with a wide range of materials, including very difficult ones, such as high-temperature metals. This makes it ideal for engineering applications where various materials are needed.
Different types of hydraulic forging presses
– Sliding-head press – A sliding-head press uses a sliding head to apply pressure to the workpiece. The workpiece is placed between the die and the moving slide head, which applies pressure and forces the metal piece to conform to the die. The slide head moves up and down to apply force on the piece in the vertical direction. – Rotary press – A rotary press uses a rotary table to apply pressure to the workpiece. The workpiece is placed between the die and the rotary table, which applies pressure and forces the metal piece to conform to the die. The rotary table rotates to apply force in the horizontal direction, thus forming the metal piece. – Toggle press – A toggle press uses a toggle mechanism to apply pressure to the workpiece. The workpiece is placed between the die and a toggle mechanism, which applies pressure and forces the metal piece to conform to the die. The toggle mechanism uses a balanced toggle bar to apply force in the horizontal direction, thus forming the metal piece. – Hydraulic press – A hydraulic press uses a hydraulic system to apply pressure to the workpiece. The workpiece is placed between the die and a hydraulic ram, which applies pressure and forces the metal piece to conform to the die. The hydraulic ram uses the hydraulic system to apply force in the vertical direction, thus forming the metal piece.
Features of a hydraulic forging press
– Press capacity – This refers to the maximum amount of force that can be applied to a workpiece during a forging operation. – Stroke length – It is the distance the ram moves before coming to a complete stop. The longer the stroke length, the more metal that can be shaped at a single time. – Ram speed – The speed at which the ram moves is important as it impacts the quality of the piece being shaped. The slower the speed, the higher the quality of the piece. – Force control – Force control is the ability to control the amount of force that is applied to the workpiece, allowing the operator to adjust the forging process. – Workpiece support – Workpiece support, or the lack thereof, can have a material impact on the quality of the piece being shaped, whether it is the die or the workpiece. Parts are shaped better when they are supported, particularly when being shaped by a rotary press.
Safety considerations for operating a hydraulic forging press
– Ensure that all safety measures are in place, including the use of guards, shields, and other safety devices. – Use hearing protection to protect your ears from the noise created by the hydraulic forging press. – Wear appropriate clothing and gloves to keep yourself safe from cuts and other hazards. – Use the hydraulic forging press in an environment with proper ventilation to prevent exposure to hazardous fumes and dust.
Hydraulic forging press maintenance
– Make sure that the hydraulic forging press is regularly maintained to prevent breakdowns and to maximize its lifespan. – Clean the machine after each use to prevent the buildup of dirt and contamination. – Have parts that are damaged or worn replaced with new ones. – Store the hydraulic forging press in a clean, dry location so that it is protected from contaminants. – Schedule annual maintenance to have the machine serviced on a regular basis.
Hydraulic forging press cost and availability
The price of a hydraulic forging press will depend on its size, brand, and other features that it may have. The price will also vary depending on the manufacturer. Hydraulic forging presses are widely available and can be purchased from both local and online stores. An important factor to consider when purchasing a hydraulic forging press is the cost of operation, which is often overlooked. You should check the operating costs, such as the cost of electricity and the cost of replacement parts, before making a purchase to ensure that you can afford to operate it. Hydraulic forging presses are available in a range of sizes, from compact models to large ones that can produce pieces up to 6 feet long. A hydraulic forging press may also be able to produce pieces that are longer, but not shorter. The price will vary depending on the size and manufacturer.
Поиск

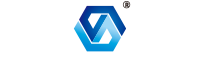
Guangdong Metal Forming Machine Works Co., Ltd.
Мы всегда предоставляем нашим клиентам надежные продукты и продуманные услуги.
Если вы хотите поддерживать прямой контакт с нами, пожалуйста, посетите Свяжитесь с нами